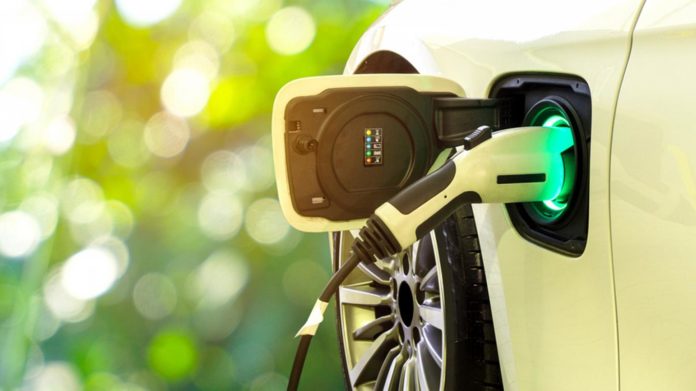
HUMANITY has begun a new chapter in its development, enabled by extraordinary technological advances commensurate with those of the first, second and third industrial revolutions. It may be difficult for many of us to comprehend fully the magnitude and speed of this change, as we only experience the effects of technological developments on our daily lives incrementally. It is only with time and perspective that humanity will fully realise the significance of the events and advances through which we are currently living.
As we move away from the hydrocarbon-based energy toward that of cleaner, renewable energy, so too industry and the automotive sector have advanced a transition from fossil-fuel internal combustion engines (ICE) to battery-powered electric vehicles (EVs). This is particularly apparent in the case of Tesla, which has seen its market capitalisation hit $1 trillion in recent days, making the electric vehicle producer the size of the other top nine leading car makers combined. Of the world’s top 20 vehicle manufacturers, which represented roughly 90% of new car registrations in 2020, 18 have stated plans to widen their portfolio of models and to rapidly scale up the production of light-duty EVs. The model availability and price range of electric heavy-duty vehicles is also broadening, with four major truck manufacturers indicating an all-electric future.
In fact, the electrification of personal mobility is picking up speed in a way that even its most ardent proponents might not have dreamt possible just a few years ago. This is being driven by the rapidly changing attitude of the consumer in the wake of both increased climate awareness and climate-focused legislation with governments championing the charge for a zero-carbon future. There is growing regulatory support for the acceleration of EV manufacturing: in July, the European Union announced in July an effective ban on the sale of ICE vehicles by 2035 as part of a broader effort to combat global warming with a 100% cut in CO2 emissions.
Further to this, US President Joe Biden has re-joined the Paris Climate Accord and has proposed spending $174bn to accelerate the shift to EVs, which includes the installation of a half-million charging stations across the country. Meanwhile, the UK has announced that it will ban the sale of fossil-fuelled combustion engine vehicles from 2030.
This is supported by the exponential growth and development in technology and battery efficiency and manufacturing. Lithium-ion batteries, the most common type of battery that power EVs and the most expensive aspect of the vehicle, are now 30 times cheaper and significantly more powerful than when they first entered the market as small, portable batteries in the early 1990s. Moreover, Bloomberg New Energy Finance projects that the cost of a lithium-ion EV battery pack will fall below $100 per kilowatt-hour by 2023, which is roughly 20% lower than today (October 2021). As a result, electric cars should reach price parity with ICE vehicles by the mid-2020s.
It is anticipated that the combined sale of EVs in the US, Europe and China will outstrip that of all other engine sales as soon as 2033. By 2045, non-EV sales will shrink to less than 1% of overall sales in those leading markets. One reliable estimate suggests that the global EV fleet could reach at least 230 million vehicles by 2030.
NEW AGE IN RESOURCE CONSUMPTION
While EVs are certainly more environmentally friendly, they are far more resource intensive, from a manufacturing perspective, than ICE vehicles. On average, EVs require six times more metals and minerals than traditional cars, much of which is used in the manufacture of the batteries.
Percentages vary depending on the battery type and model of vehicle, but a single car lithium-ion battery pack (of a type known as NMC532) typically contains around 8kg of lithium, 35kg of nickel, 20kg of manganese, and 14kg of cobalt, according to figures from Argonne National Laboratory, a multi-disciplinary science and engineering research centre linked to the US Department of Energy.
When these numbers are multiplied against the projected growth of EVs in the coming years, the conclusion is simple: the phenomenal tonnages of materials required in the manufacture of EV batteries will spur a surge in demand and production of these materials on a scale that will characterise a new age of resource consumption.
Nickel-manganese-cobalt oxides (or NMCs) are among the most important storage materials for lithium-ion batteries as they offer higher energy density compared with batteries without nickel and are a good fit for larger EVs going longer distances. In 2021, the manufacture of NMCs has achieved mass-market scale and accounts for more than 60% of the EV battery market share. As such, many analysts do not anticipate a move away from this type of battery any time soon.
However, there is considerable research and development being undertaken to improve these batteries, in the main to reduce the amount of cobalt required, a chemical element that is not only the most toxic component, but the mining and sourcing of which is mired in some controversy.
With nickel supply constraints looming, more work is being done to further increase the overall percentage manganese in the makeup of EV batteries on account of the fact that it is a safer, more abundant and stable material. Further to this, the low price of manganese, c. $6,000/t, relative to nickel and cobalt, $20,000/t and $60,000/t respectively, make it an attractive alternative.
MANGANESE: AN OVERLOOKED OPPORTUNITY
EV battery manufacturers require a high-purity form of manganese, known as manganese sulphate monohydrate (HPMSM). Unfortunately, the bulk of the current production of this type of manganese, which is dominated by China, is plagued by environmental concerns and it is largely produced through the conversion of high purity electrolytic manganese metal (HPEMM), which is highly energy intensive.
As China naturally lacks resources of high-grade manganese, much of the country’s EMM production is derived from lower-grade manganese ore, which needs to be concentrated in order to reach the desired level of purity. This is accomplished by burning off impurities, a process that creates air pollutants. The high power demand which is then required to convert HPEMM to HPMSM is often sourced from domestic coal-fired generation, which produces high amounts of carbon dioxide. It therefore stands to reason that the lower the grade of manganese ore used as an input, the greater the pollution by-products generated.
Environmental concerns are not the only challenge to the production of HPMSM and HPEMM. The other major challenge is supply, evidenced by the fact that China has been experiencing a widening year-on-year manganese ore supply deficit for the last two decades. It is also worth mentioning here that the supply chain of critical metals is of paramount importance for western based automotive companies, such as Tesla and Volkswagen, as they work to demonstrate their green credentials and sustainability, both in the end product delivered and in the production thereof.
This bid to solidify supply chain and material sourcing means that there are significant opportunities for new companies operating in other manganese-rich mining jurisdictions to fill this supply gap and take advantage of the surging demand for this critical and ’forgotten’ battery metal. However, there is an important caveat to this: the technological barriers to entry are high and the development of new HPMSM projects, despite the geological proliferation of manganese, is reliant on high grade targets with complex metallurgy and processing requirements.
Robin Birchall is CEO of Giyani Metals which is finalising a feasibility study to produce around 120,000 tonnes of HPMSM from a project in Botswana, coming into production in 2024.