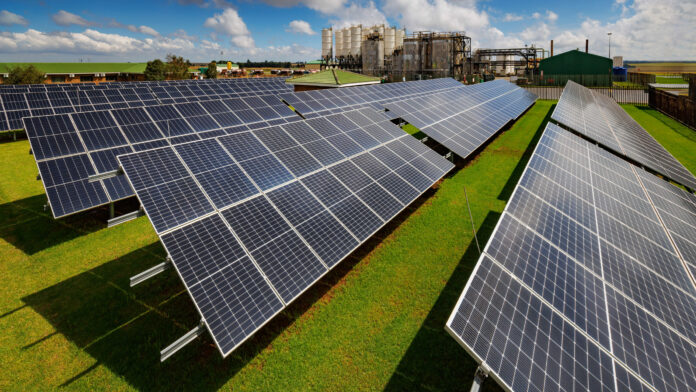
BME, a division of JSE-listed Omnia, has cemented its position in South Africa and globally through a relentless focus over 40 years on innovation, enabling it to offer customers products and services that enhance efficiency while reducing their environmental footprint.
Ralf Hennecke, Managing Director of BME says, “Innovation plays a big role in ESG and where we can contribute the most is through the mining cycle. While reducing our direct emissions in the manufacturing and blasting process is important, if we can optimise blasting we help our customers reduce their carbon emissions.”
BME manufactures and supplies explosives as well as mining chemicals and provides technical services and value-add technology to the mining, quarrying and construction industries. Its products include bulk emulsions, packaged explosives, initiating systems and mining process chemicals. Its technical services range from digital blast monitoring to advanced consultancy and optimisation projects to provide cost-effective blasting, increased mineral recovery, higher plant throughput rates, reduced waste mining and longer life of mine.
Sustainability underpins BME’s research and development and with innovation in its DNA, it has developed products such as Innovex™ formulations that recycles used oil and a dual-salt formulation that enables the manufacture of finished products at lower temperatures, resulting in reduced energy consumption during the production process. BME’s AXXIS™ is the most accurate detonating system globally.
Hennecke says if BME optimises blasting to such an extent that it enables other service providers to load and haul more efficiently – which ultimately optimises the process through the mill, plant and refineries – that will deliver a major benefit for customers, because the loading, the hauling and the plants generate a lot more carbon than BME’s explosives.
“Where we can add value is through accuracy, through our products, to ensure precision blasting that will benefit downstream all the way to the plant. That is what new technology and digitisation means for us,” Hennecke says.
He added that real time reporting, blast data collection and storage and blast data analysis enables predictability in blast outcomes and ultimately leads to blast optimisation for subsequent mining cycles.
A game changer for BME and its global mining customers is Omnia’s investment in Hypex Bio, a Swedish company, which has developed the first industrial-scale offering of a hydrogen peroxide emulsion (HPE), a long-awaited alternative to traditional nitrate-based explosives.
HPE offers an equivalent performance to ammonia nitrate explosives while enabling miners to reduce their environmental impact compared to traditional blasting methods, enhance efficiency, and reduce costs. As more companies commit to decarbonising their value chains, this technology has the potential to transform the explosives supply industry.
Hennecke says the mining industry is slow in adopting change. In terms of the use of explosives over the last 150 years there has only been three major changes, from ammonia nitrate fuel oil (ANFO) to packaged explosives (water gels and emulsions) and then pumpable emulsions. Likewise, detonators have progressed from cap fuse to non-electrics to electric and then electronic detonators.
Hennecke says the investment in Hypex Bio and the future collaboration opportunities with the Swedish business has reignited the drive at BME to find new and better ways for its customers to mine.
BME is now on a new trajectory and the mining industry has noticed.
Hennecke says “all tier one miners that we are associated with have approached us with interest in Hypex Bio’s HPE offering.”
Hypex Bio provides a solution for customers to comply with mining licensing requirements, reduce their impact on host communities, preserve ecosystems, and contribute to their own and their country’s ESG goals.
“For mining companies to meet their emissions targets, they need to reduce their impact during blasting, so there needs to be a change,” says Hennecke.
HPE truly differentiates BME. The manufacture of HPE explosives offers a significant reduction in total carbon emission and elimination of ammonia residue as compared to nitrate-based explosives. Based on the current European Union average manufacturing 1kg of ammonia nitrate emulsion phase emits 2.3kg of CO2, while 1kg of HPE emits 0.23kg of CO2 – a 90% difference.
HPE, which has passed regulatory tests and is approved under the European Union Civil Explosives Directive, is free of nitrates and ammonia and so offers many environmental advantages.
As the hydrogen peroxide acts as an oxidiser without producing ammonia and nitrate by-products like nitrogen oxide (NOx) gas, there is no potential for NOx fume clouds following blasts, which can impact a licence to operate. Likewise, environmental permits for new sites may be secured more timeously given the improved emissions profile for mines using the Hypex Bio system.
The use of HPE enhances efficiency as it is unlike ammonia nitrate-based explosives that can only be deployed during favourable wind conditions to avoid NOx clouds impacting nearby communities. When explosives based on ammonia nitrate are used underground efficiency is impacted by the time spent waiting for post-blast fumes to dissipate.
In addition, explosives free of ammonia nitrate (and other nitrates) can reduce water treatment costs and water impacts, as there is no aqueous nitrate and ammonia discharge requiring remediation.
The emulsion is currently suitable for use in locations with cold climates, while in hotter areas tests are underway on the storage requirements of the product.
Hennecke says “Hypex is not only about one invention. It’s about numerous co-developments and opening doors for us on many fronts. Hypex is groundbreaking, watch this space.”